Individual project
The project consisted in a Design developement of an orginial EVtol concept. The project was developed in what would be considered the cruise mode of the vehicle at the subsonic speed of 200km/h, making it incompressible. The design changes consisted in playing with the span and wing location, and reducing the drag by locating some vortex generators at the rear of the vehicle.
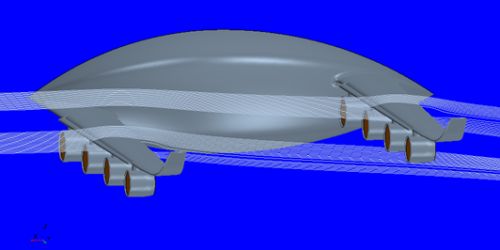
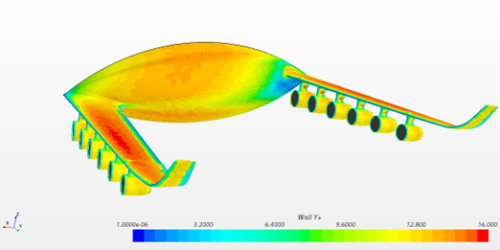
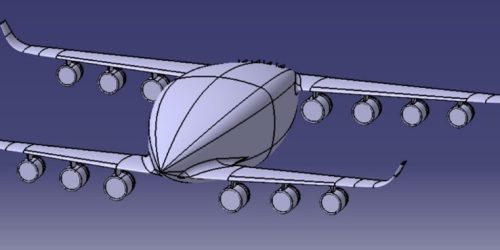
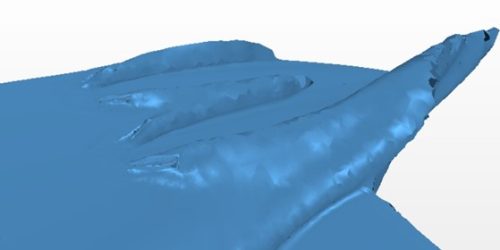
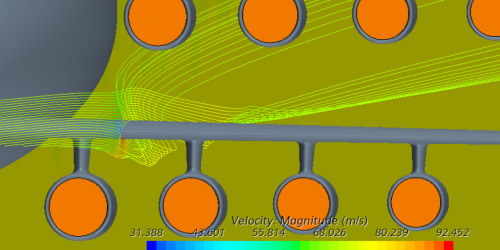
– The final desing made a significant focus in the interaction between the two wing and how can this one be reduced.
– The design was fully developed with CATIA v5, the shape had to be imported to the CFD software and some surface repair had to be done.
In the CFD part, all the simulations were made with the comercial software Star CCM+. The model was validated with mesh independency studies and Y+ treatment.
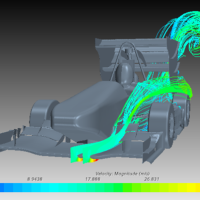
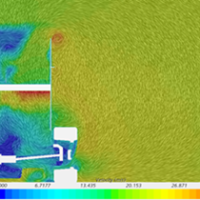
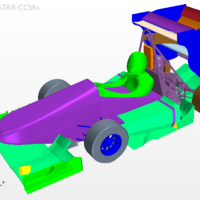
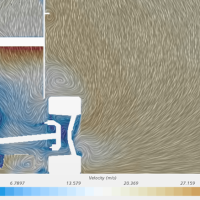
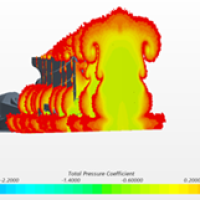
Formula Student project
This project was also a design developement project, but made in group with the colamboration of my classmates. The design of the whole car was divided in to different sections and developed individually by the team members. CATIA v5 was used for the design of each component and put together in an asembly. The software used for the CFD simulations was Star CCM+.
The different components interact aerodynamicly such as the front wing would seal the gap between the bottom of the rear wing endplate and the wheel, or the rear wing creating a low pressure effect at the floor exit, helping the air to be sucked.
The deisgn improvement in the rear wing consisted in a series of small improvements that resulted in an overall substantial one. The first one consisted in changing the locations of the wings and adjusting the gaps. The top wing was divided in to two smaller ones that allowed to increase the downforce without compromising the drag by creating a new gap. Also, vorterx generators were added at the endplates to reduce the induced vorticity by pressure difference between the insider and outsider sections of the endplate.
Other projects
- FEM/FEA projects:
The projects were based on structural analysis of aircraft and rocket components, such as combustion chambers, doors, structural components and reinforcements. The materials simulated were isotropic and anisotropic (composites). The analysis were focused on stress analysis and design optimization, where topological optimizations were performed and different technical issues were treated such as singularity and mesh inaccuracy issues.
- Python and MATAL discretization projects:
This projects consisted in discretizing the formulas based in shockwave theory and wing theory for doing analisys on diffent wings at subsonic and supersonic conditions. The discretization method was fully performed using Python and MATLAB scripts made from zero.
- Turbine stage design of turbomachine:
This project consisted in optimizing the airfoil of the turbine stage of the Siemens SGT5-4000F by using first analyitical modeling to create the preliminary design, and optimizing the design with CFD iterations.